Linear Actuators and Their Role in Automation
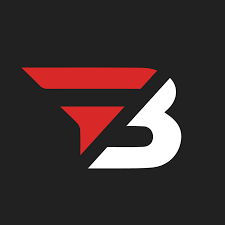
Admin
AI Research Analyst | 31 January 2025Table of Content
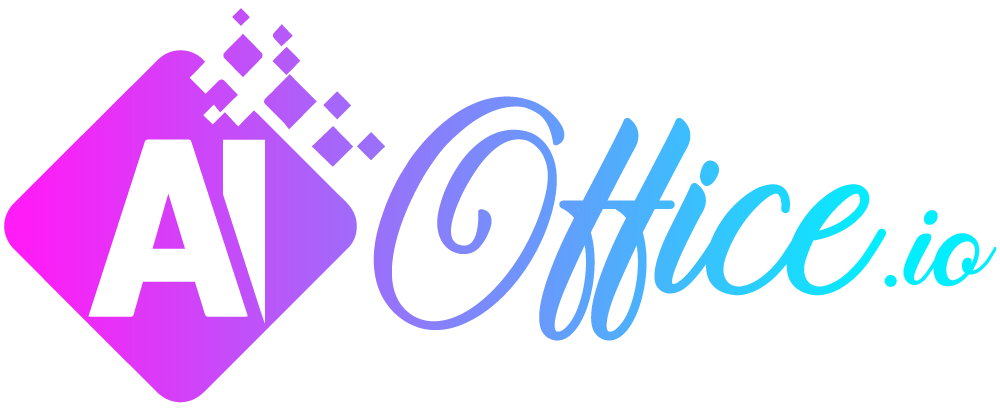
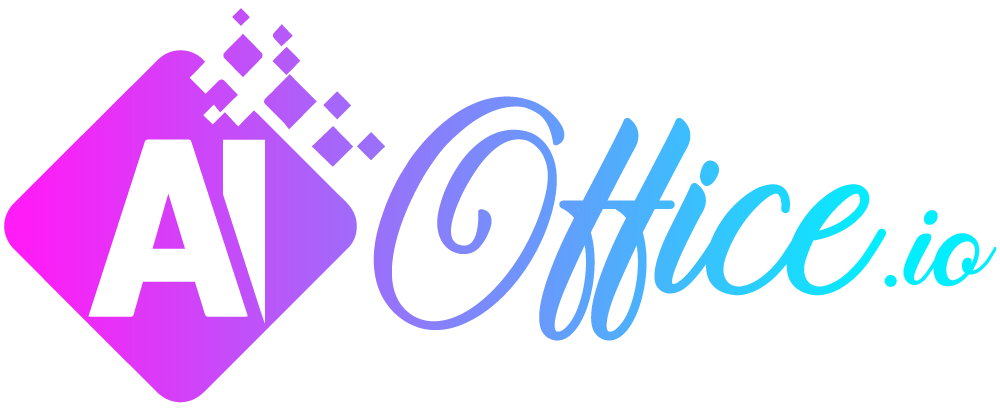
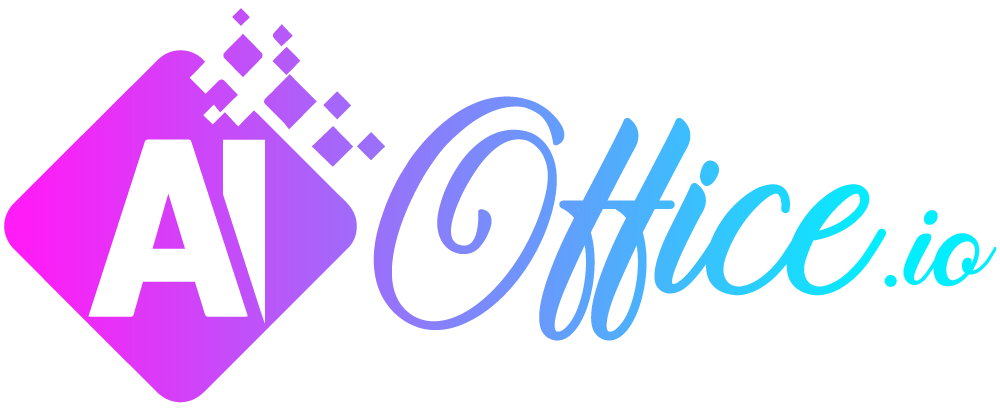
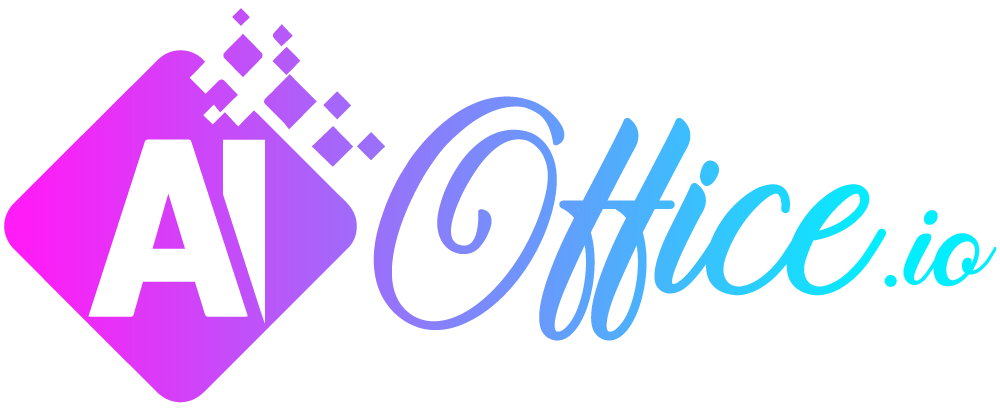
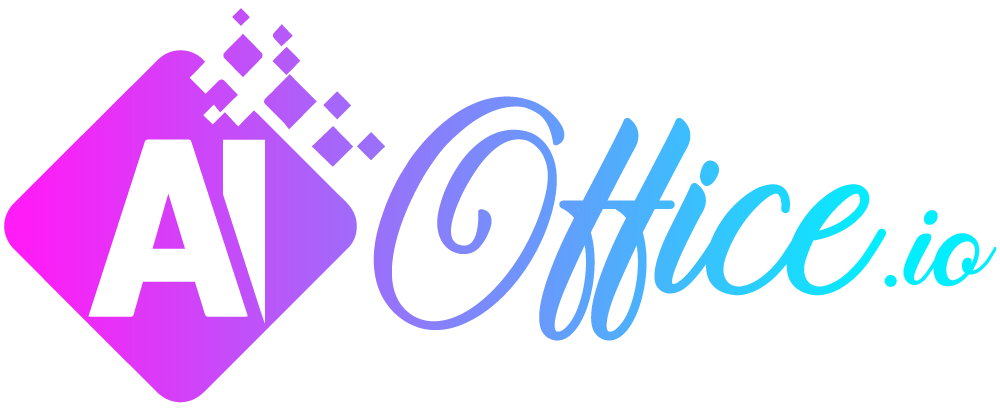
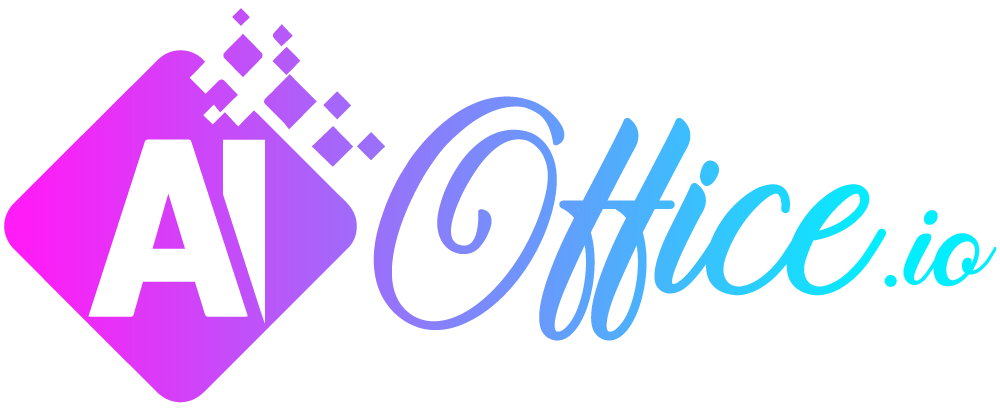
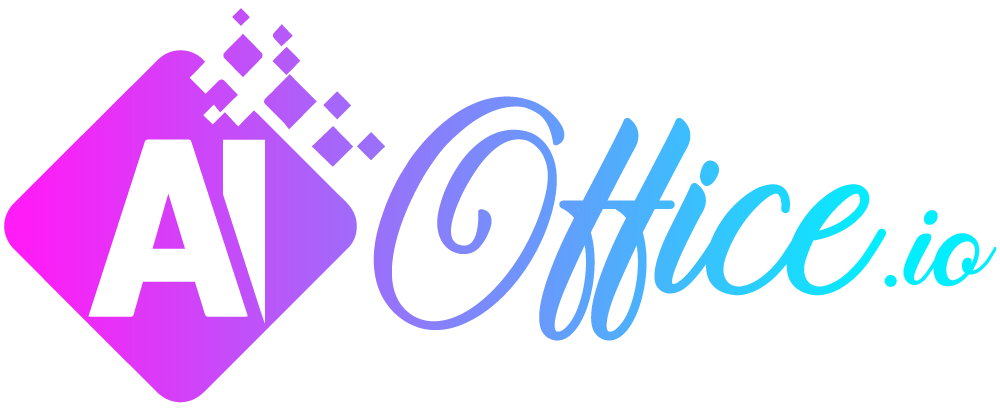
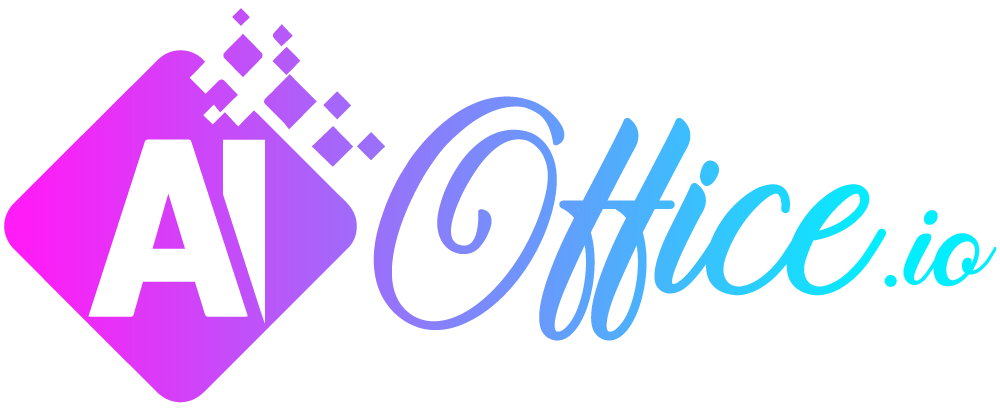
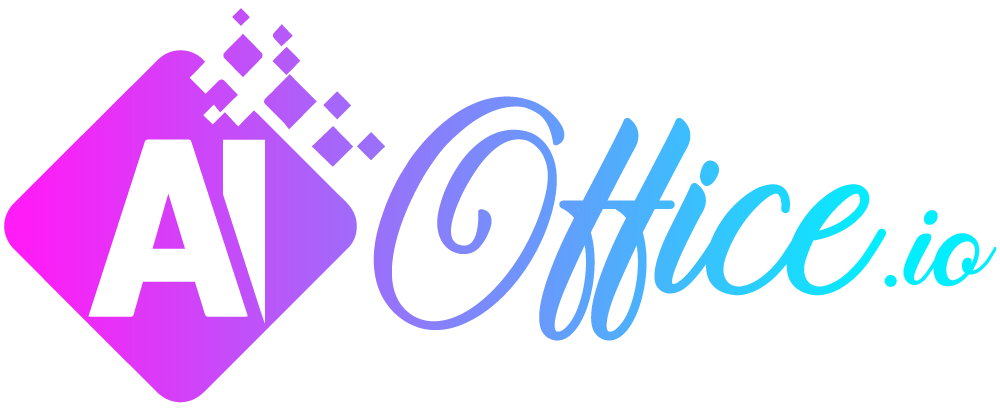
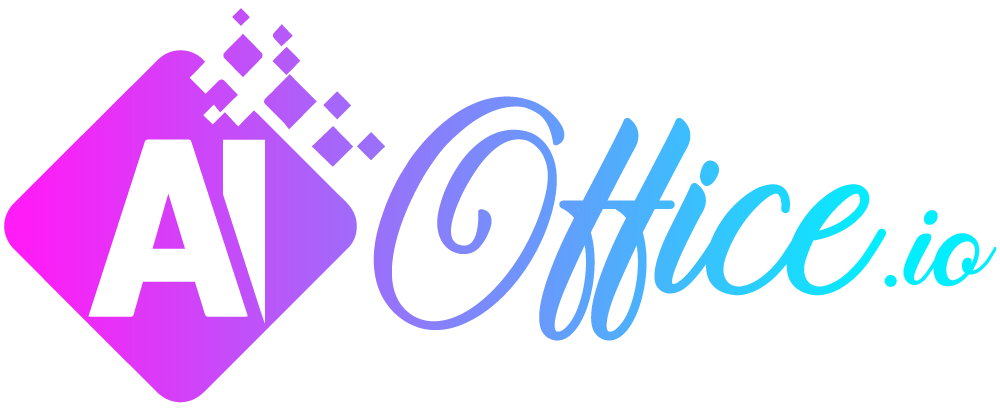
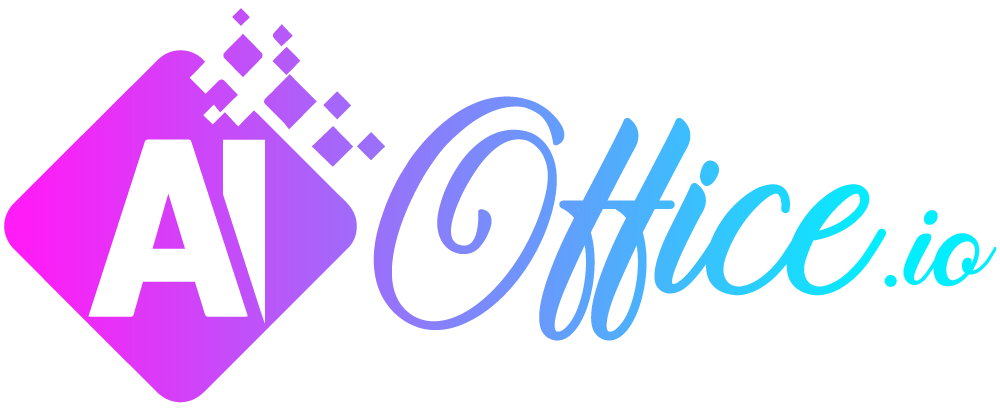
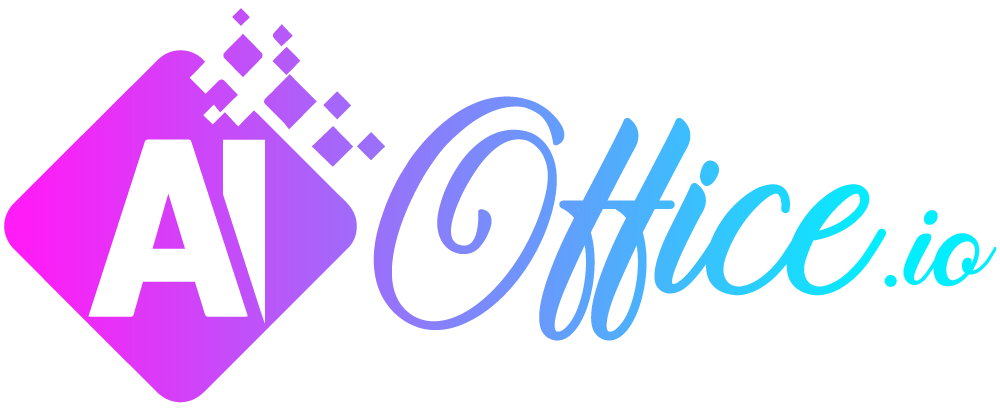
Linear actuators function as essential components in robotic systems and industrial automation machinery. These actuators provide vital movement capabilities that all moving equipment needs, no matter what actuation system operates.
These actuators support practical tasks and safe control operations for different applications, such as production and testing, material movement, machine adjustment, and control management. Identifying the correct actuator for your machinery requires a critical decision.
How a linear actuator works
The mechanical device, a linear actuator, transforms rotary motion into direct linear motion. The device includes multiple elements that collaborate for precise straight-line movement. The electrical motor is a starting point because its DC or AC operation produces rotatory motion. A gear reduction system transforms incoming power to generate increased torque and slower speed, enabling powerful applications.
Linear pneumatic actuators serve basic motion profiles while operating standard industrial automation equipment. They execute tasks such as material handling, robotics operations, and clamping and indexing procedures. These systems use compressed air to create mechanical movement but maintain easy assembly procedures.
The cost-effectiveness of pneumatic actuators makes them suitable for low-force operations. However, their performance precision is lower than that of electric actuators, and their durability is less favorable than that of hydraulic actuators. Pneumatic actuators suit applications that need basic control systems because they frequently support linear actuator systems used for lifting objects or material handling processes.
Types Of Linear Actuator
Linear hydraulic actuators
Linear hydraulic actuators, or hydraulic cylinders, are used in powerful clamping, positioning, lifting, and pressing tasks. Due to their high force density, hydraulic power is employed for mechanical operation, making these circuits relatively fast, robust, and powerful. Cylindrical actuators are typically used for high loads, and their additional duties and applications include serving as linear actuators in durable beds and lifting stages.
However, hydraulic actuators are not as accurate as electric actuators, though this can be improved without expensive components like servo valves. Additionally, hydraulic fluid leakage is an inherent issue that poses safety concerns for operators and the environment.
While hydraulic actuators are strong and reliable, they are not very efficient, require frequent maintenance, and have significantly higher operating costs than other actuators. A position feedback type of linear actuator may be necessary to achieve better accuracy in hydraulic systems.
Electric Actuators
Electric actuators are known as electromechanical actuators (EMAs). These tools are operated by electricity and have mechanical parts like screws, gears, or belts for operating and lasting force. These actuators enable precise position control, are programmable, and exhibit energy efficiency. They also have limited flexibility regarding the length of their stroke and the speed at which they move it. Motion simulators are one example of the flexibility of electric actuators for use in motion control applications.
However, shock loads quickly damage EMAs; they undergo shock loads from the mechanical parts that wear their metal parts, giving metal-to-metal wear. Electric actuators with encoder feedback are possible, and they enhance the motors' accuracy. Electric actuators are also more costly than other forms, especially in higher-force variants, and require consistent relubrication.
Lead screw mechanism
The lead screw mechanism serves as the core functional element of actuators because it rotates a threaded rod to drive a nut toward the rod's end. The actuator executes linear motion by moving its rod and stick through an extending or retracting method. Linear actuators usually have built-in limit switches and position sensors. These features help users work safely and accurately.
Multiple industries use these devices for controlled linear motion functions through compact frameworks.
How Linear Actuators Work in Modern Machinery
A linear actuator is essential in the automation field since it turns energy into a straight movement along a line. When looking into the question ‘What is a linear actuator and how does it work?’, one discovers that such handy devices operate a range of applications from plain devices to complicated production systems. Some of the current features in modern architecture are linear actuators equipped with position feedback and intelligent controls to run them.
Common Applications and Uses
Further, understanding the utilization of linear actuators demonstrates that these systems are beneficial.
- Creating TV lifts for home automation
- Powering standing desk mechanisms
- Using automated doors with linear actuator door openers
- Helping motion simulator systems
- Helping adjustable bed frameworks
Key Performance Considerations for Selection
Force and Load Management
For a linear actuator mechanism, engineers choose the load profile as one of the options available for the mechanism to use. In each of these linear actuators, whether using a hydraulic linear actuator for moving heavy loads or an electric linear actuator to move objects with high precision, it is necessary to get familiar with force demands. In some cases, it is necessary to use linear actuators with force feedback, for example, for accurate positioning.
Speed and Control Systems
Modern applications can integrate linear actuators, Arduino control, and complex positioning systems. The stroke length of the linear actuator determines the working speed and the extent of movement in the design. When more exact movements are needed, linear actuators with encoders or position-control linear actuators are often used.
Precision and Feedback Systems
In today’s automation applications, it is common to call for linear actuators with potentiometer feedback or any other position-sensing system. It's especially important where high precision is necessary, probably in positioning planes and satellites, among other uses. Some systems use limit switches with linear actuators to guarantee secure and accurate working ranges.
Durability and Maintenance
Pneumatic and electric linear actuators must be durable, no matter which kind is used. Proper linear actuator maintenance minimizes possible problems, but some may develop and require professional help.
Smart Integration
- Modern manufacturing systems often incorporate linear actuators controlled by IoT-capable controllers. Such intelligent systems commonly consist of linear actuators that can be operated and controlled remotely.
Challenges of Linear Actuators in Automation
Environmental Impacts
Using linear actuators in automation encounters several problems, affecting their performance and durability. Externally, the working environment is sensitive because dust, temperature fluctuations, and moisture affect performance and wear rates.
For example, the conditions may particularly impact electric linear actuators' electrical parts and lubrication systems.
Precision and Control
Another considerable concern is achieving accurate position control, particularly in applications where attenuation is vital. Systems that employ linear actuators with position feedback are vulnerable to drift and calibration at set intervals.
Another challenge is integration complexity, such as integrating advanced actuators into legacy systems or harmonizing two incompatible protocols.
Maintenance and Technical Limitations
Maintenance requirements present constant problems; accessibility is a problem; the repair of the linear actuator requires special skill and, therefore, is another problem.
This trade-off between speed and accuracy frequently involves fine-tuning, where increasing speed undermines accuracy. Also, one type may have limitations peculiar to it – so hydraulic linear actuators may pose problems with fluid leakage. In contrast, pneumatic linear actuators may have issues with accuracy.
Cost and Future Considerations
There is always the issue of costs, including capital expenditures, operational costs, maintenance, and training. Another layer of difficulty is constantly upgrading and ensuring compatibility with new automation technology standards, which creates more hurdles in these tasks.
Final Words
Thus, linear actuators remain critical elements of modern mechanisms and robotic equipment as automation progresses. These devices offer smooth, consistent movement to drive countless industry processes, from essential push-pull components to complex computer-operated actuators. The convenience and reliability of linear actuators cannot be overemphasized in manufacturing facilities, medical equipment, and home automation, among other applications.
As new technologies emerge, they introduce smarter actuators with better feedback mechanisms and IoT capabilities, broadening the possibilities for full automation. The linear actuation of the future will be even more accurate and smarter, incorporating new and advanced features that will change how the world is automated.