What is Dedicated Spindle Software
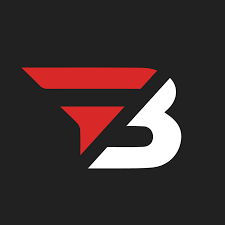
Admin
AI Research Analyst | 07 February 2025Table of Content
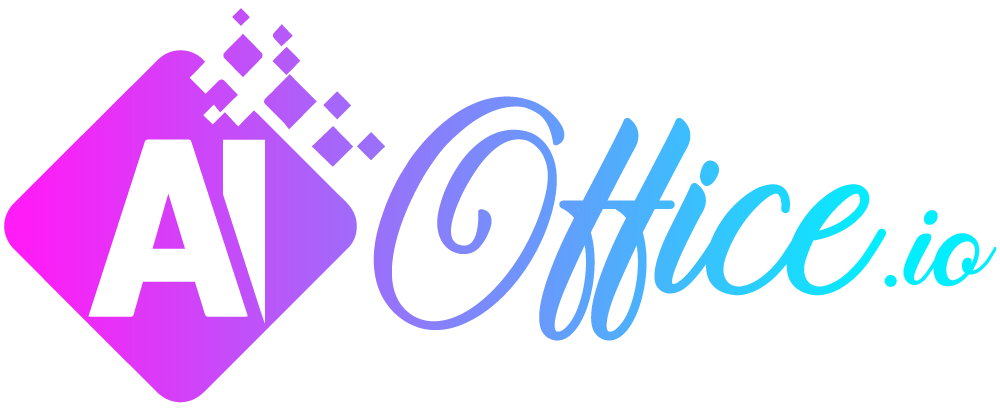
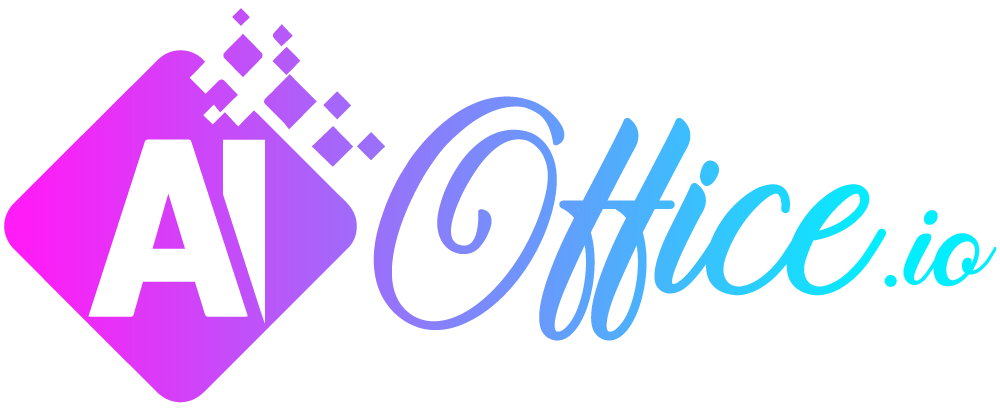
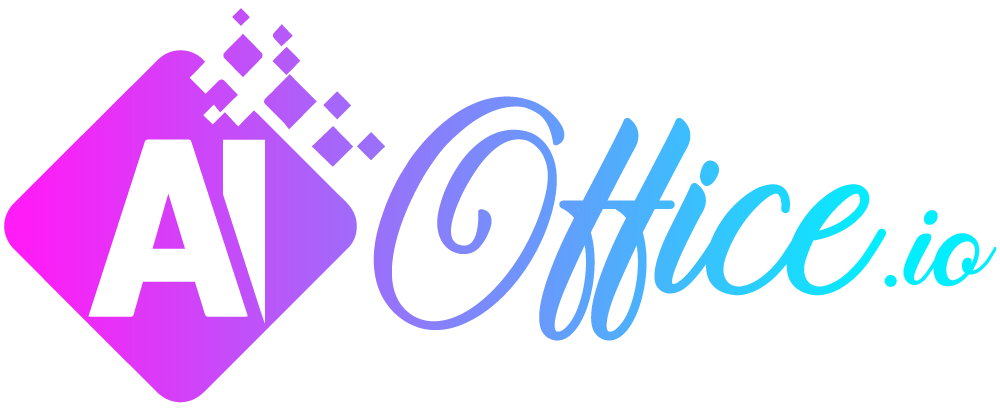
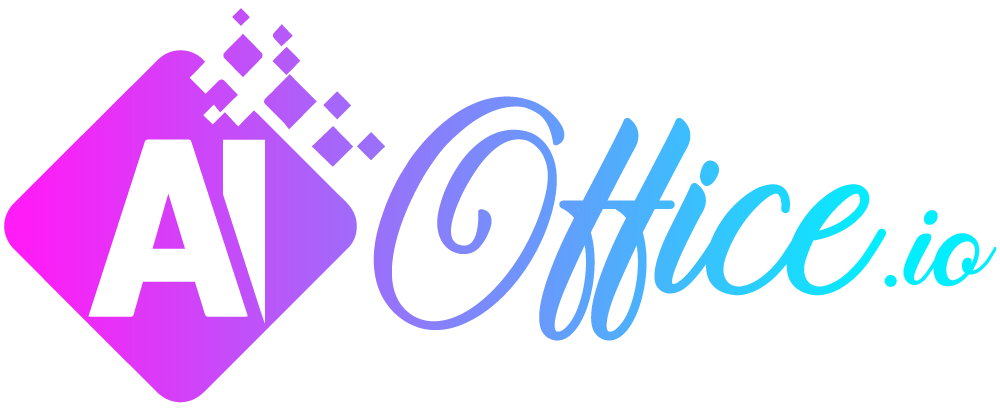
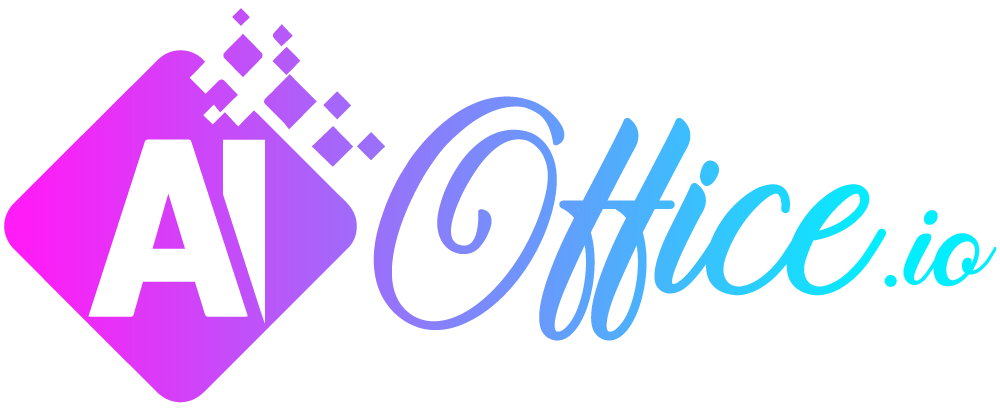
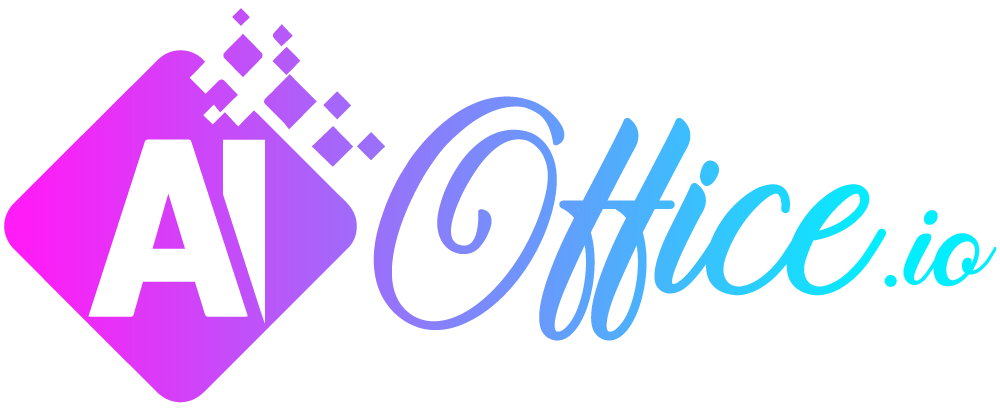
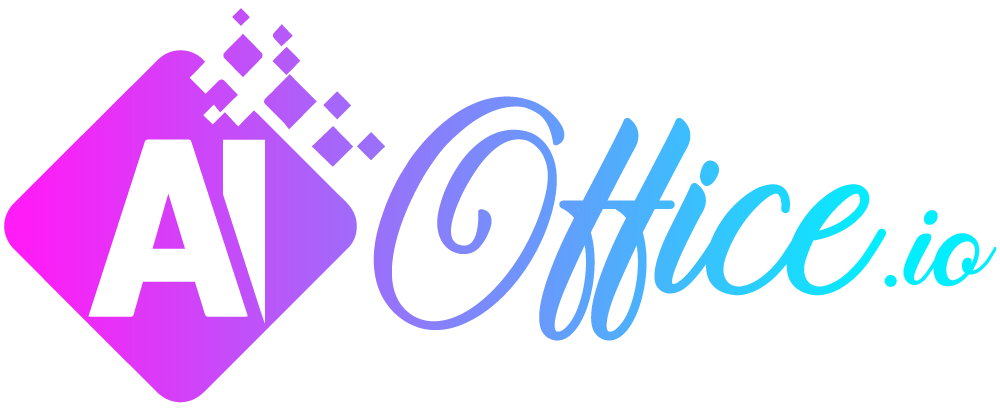
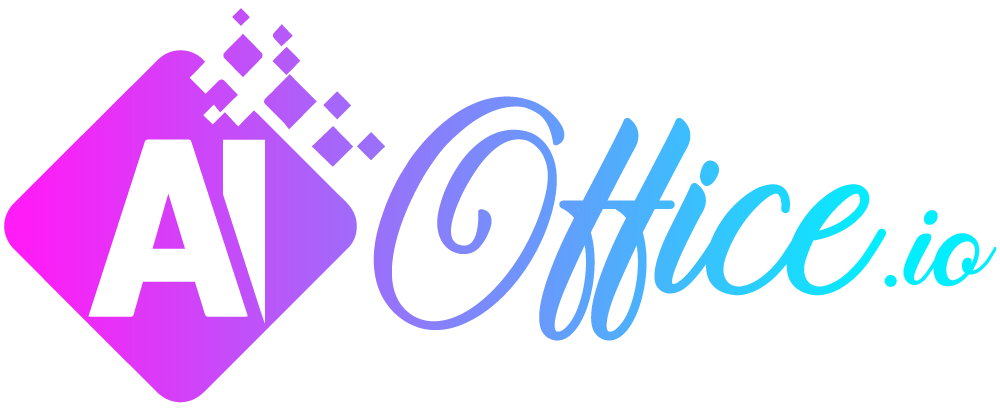
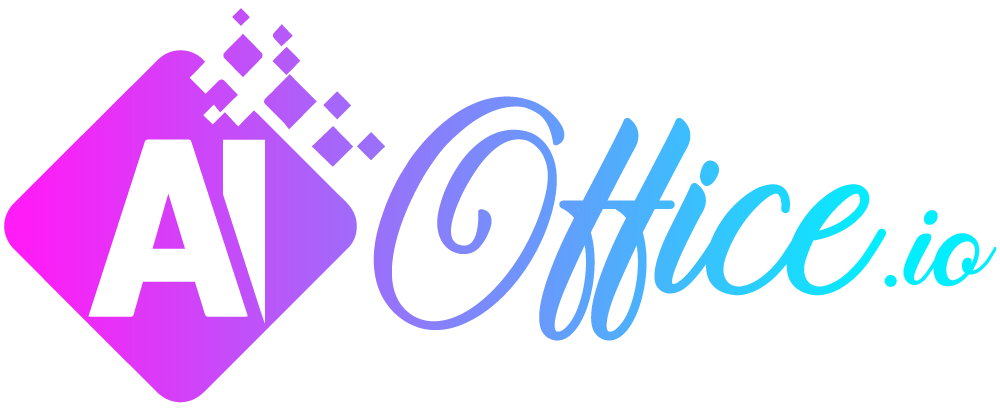
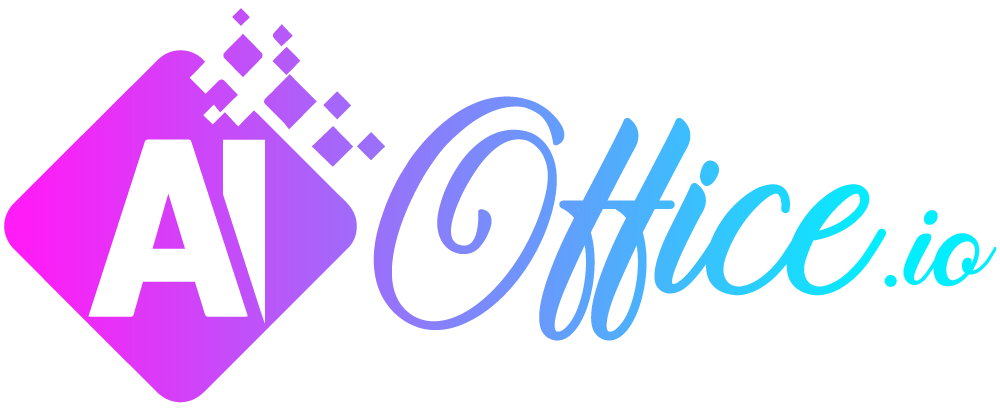
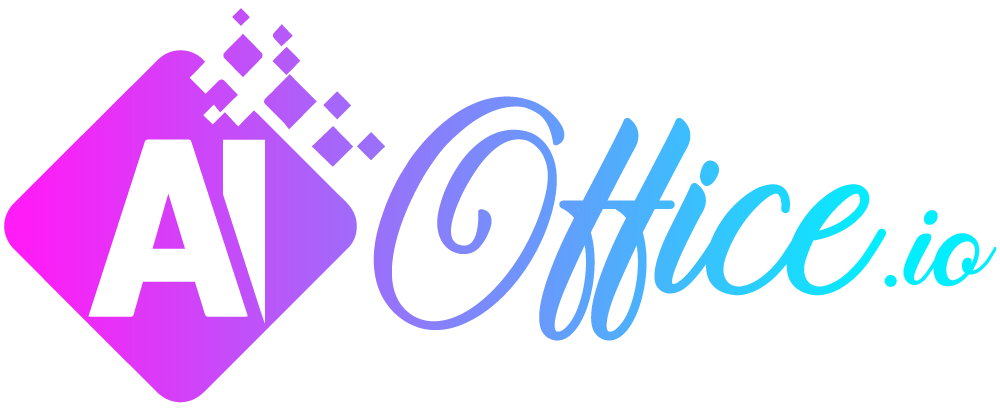
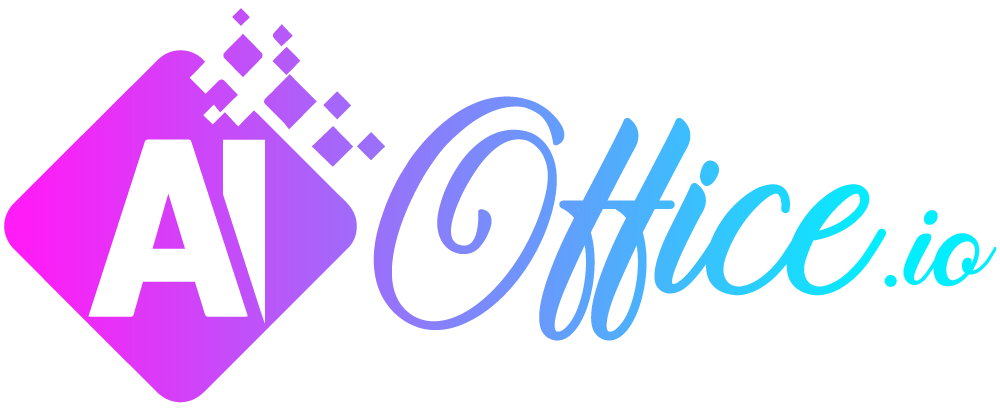
Delicate spindle software has changed the way we use CNC machines and others. Don’t consider it simple software; it helps machines to operate accurately and without error.
Whether working on a CNC machine or in manufacturing, understanding delicate spindle software is important for improved work efficiency. In this article, we will first explore CNC machines, followed by spindle software, and finally discuss their benefits and the broader impact of this informative technology.
What is a CNC Machine?
We must examine CNC machine functionality before studying software because this knowledge will simplify our software education. The CNC (Computer Numerical Control) machine performs physical operations through computer-based control systems.
Just as AI is becoming more fully integrated into companies, and delicate spindle software is its example. It operates in factories, performing drilling, cutting, and other tasks through software. In this case, only computer instructions are provided, and people are not involved.
How Delicate Spindle Software Helps Here
After understanding the workings of the CNC machine, let's see what role the spindle software plays here. Actually, it handles the spinning portion of the machine. It controls how the machine moves and spins, which is also called the spindle.
This software continuously inspects the cutting moment of the machine, ensuring the cutting is accurate. Not only that, but it also automatically manages any overhead-related issues. This software makes the CNC machine more accurate.
What are the working Features of Delicate Spindle Software?
Monitor Tool Wearing
Some advanced monitoring tools help you monitor the broker parts of a machine and analyze when you should replace these tools. This gives you an idea of which parts to replace and when.
Control Overheating Issue
It’s the best software to increase the shelf life of the machine. Overheating is the main factor that leads to reduced shelf life, regardless of the type of machine. One of the main features of this tool is that it handles overheating; it monitors the machine and alerts the system to stop operating when overheating occurs. This helps extend the shelf life of the machine.
Generate Automatic Reports
Technik records operational data for analysis and generates reports from this information throughout extended periods. Manufacturers can track performance patterns, detect improvement opportunities, and stay compliant through the software's data logging system.
Alerting System
The system allows operators to create selected alerts together with notifications for particular system conditions like speed variations or changes in machine load. The system enables proactive CNC machine control and fast resolutions for developing potential issues.
How to Select the Best Spindle for Steel and Aluminum Machining: Advice and Cooling Choices
The correct spindle is crucial when machining steel or aluminum. Here are some recommended spindles for better results. Typically, spindles designed for routers are planned for cutting wood & plastic; they are unsuitable for machining steel.
There is no doubt that these spindles can work on machining aluminum, but you cannot achieve optimal results with them. Generally, people recommend milling machines because they are specifically built to handle the demands of steel machining. On the other hand, milling machines provide better stability and can perform operations at lower speeds with high torque, making them effective for hard materials.
Cooling Options: Air-Cooled vs. Water-Cooled
Testing shows users have alternating opinions about the cooling options available to them. Water-cooled spindles help users while they operate because they provide effective cooling & silent operation. Some users think water-cooled spindles require complex maintenance steps because they need water circulation systems, according to some users that a former water-cooled spindle user made an improved switch to air-cooled technology because maintenance proved less complicated.
Installation and maintenance of air-cooled spindles remain straightforward, but users doubt their operational performance when operating at low speeds.
An air-cooled spindle rapidly heats up during extended work sessions, according to some peoples feedback about the machine's continuous operation. Remember this key factor to meet your machining needs when choosing a spindle.
What Are some drawbacks of Delicate Spindle Software?
Complex Software
Delicate software is complex software; therefore, the user must have necessary information about both the machine and the software. Without training, a person cannot use this software.
High Sensitivity to Environmental Conditions
Delicate spindle software functions best when sensors and systems supply it with highly accurate inputs. External environmental factors which disturb the machine operation will negatively impact the software performance and result in both errors and subpar efficiency.
Not Ideal for Heavy-Duty Applications
A precise set of commands focusing on light-duty tasks represents the main purpose of delicate spindle software development. The software has difficulty managing intensive machining operations, which require high torque strength and high durability when dealing with hard materials like steel. The software becomes inappropriate when manufacturing operations that demand powerful machining systems.
Customization Limitations
The software does not provide enough options to customize the system. The adaptation of software to process special machining requirements and individual workflow configurations becomes difficult for operators thus hindering productivity improvement during non-standard operations.
Downtime During Updates
The updating process of sensitive spindle software leads to reduction of operational flow. Production interruptions caused by software updates become common when the updates need CNC machine reconfiguration and spindle recalibration.
Dependency on Manufacturer Support
The maintenance of sensitive spindle software systems usually needs manufacturer technical support for debugging and sophisticated system configuration tasks. The manufacturer’s delayed support or total unavailability creates delays in solving problems that affect production times.
Limited Scalability
The software lacks capability to expand operations when manufacturers use multiple CNC machines within their manufacturing processes. Using single software to operate numerous machines equipped with individual spindles results in an inefficient and unmanageable situation.
Energy Consumption Concerns
Setup requirements with real-time diagnostic functions and sensor operation in delicate spindles tend to consume extra energy due to the continuous processing demands. The continuous use of these machines would boost operational expenses across the period.
Conclusion
CNC machines have a very important role played by the delicate spindle software. If you learn the basic skills to use it, it can double your productivity. However, learning it can be a bit complicated. In 2024 and in the future, its scope will increase, and more advanced features can be added to it, because the next era belongs to AI.