What is Operational Technology?
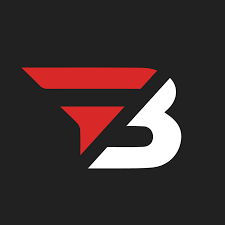
Admin
AI Research Analyst | 15 November 2024Table of Content
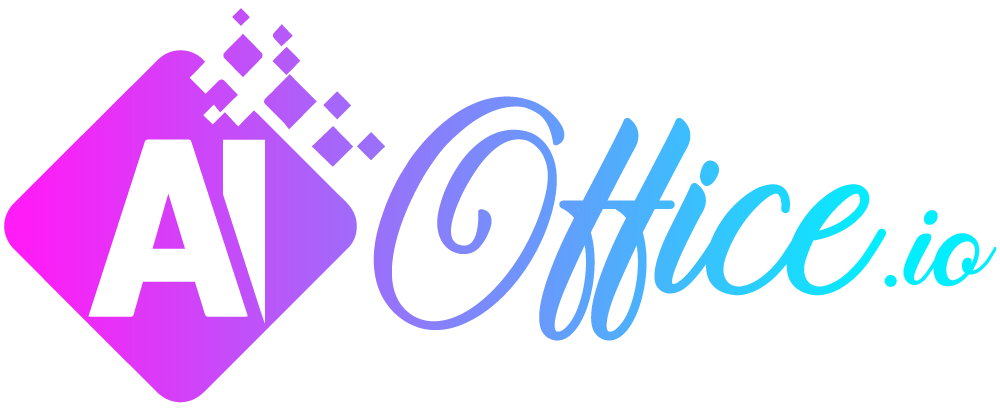
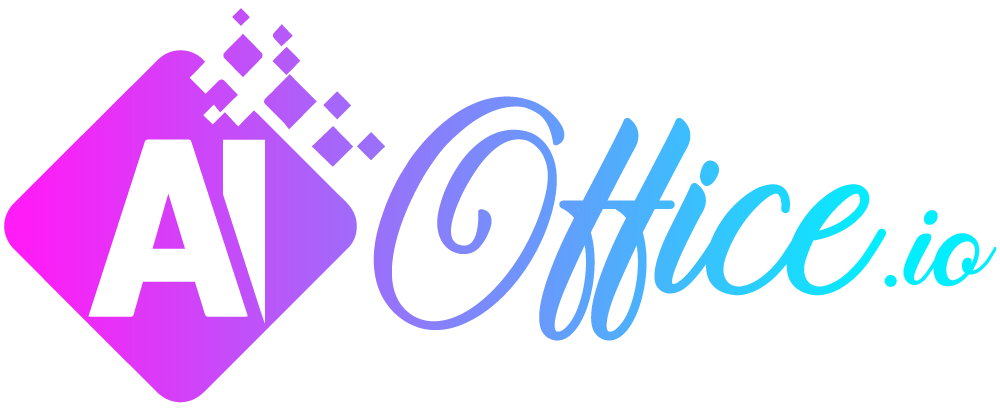
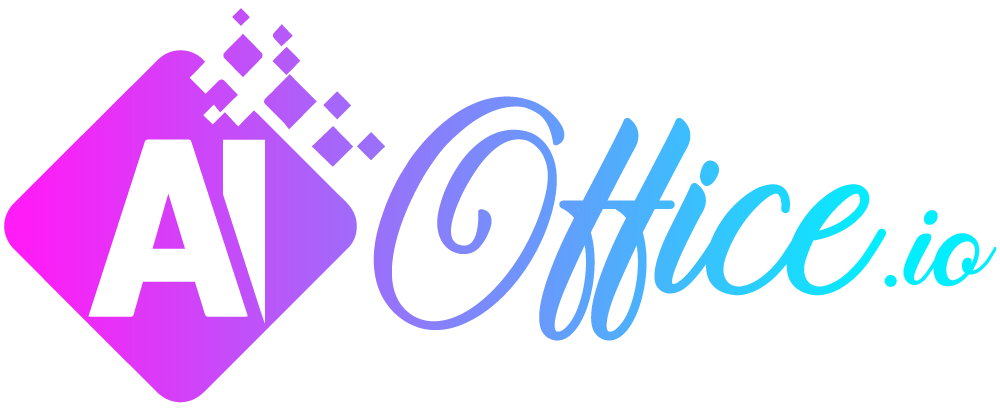
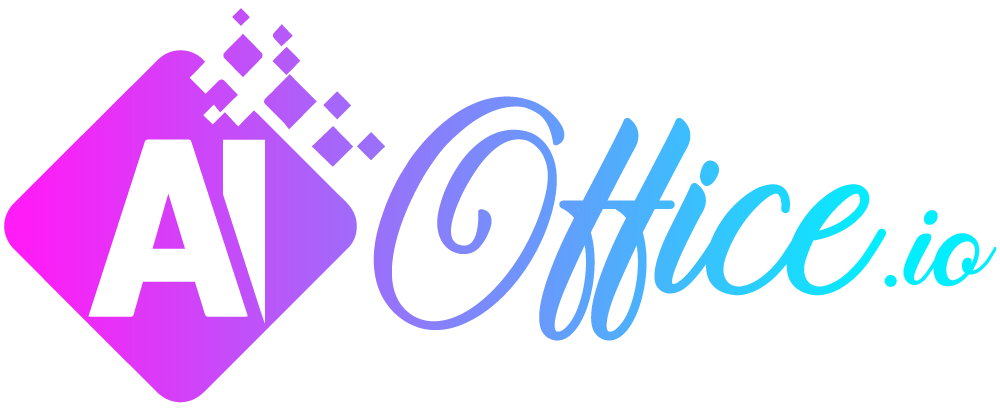
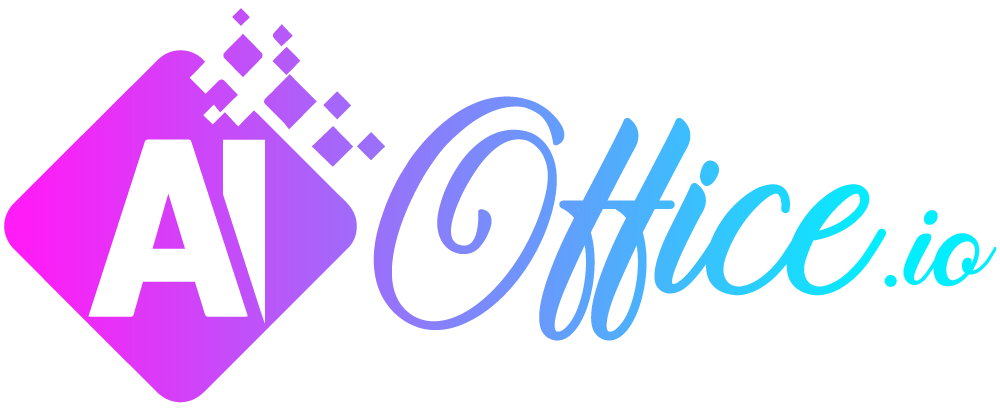
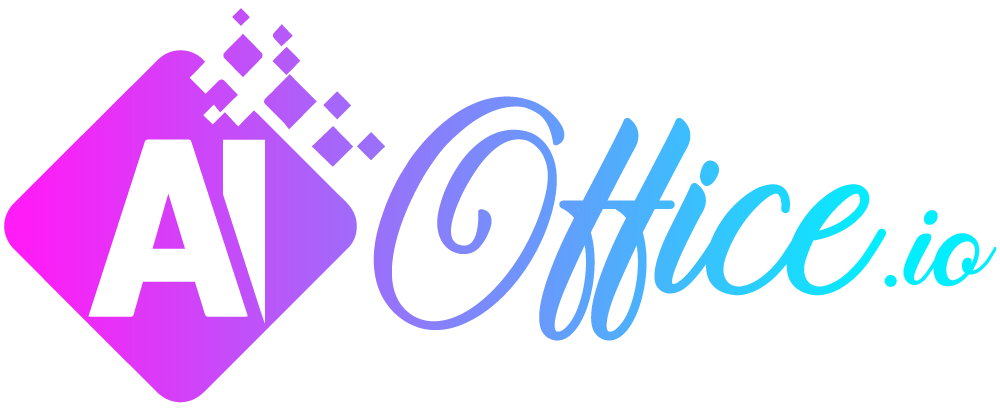
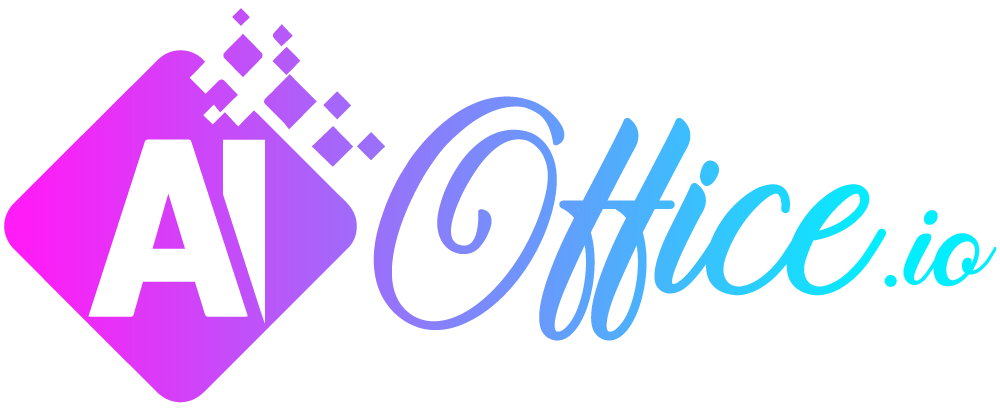
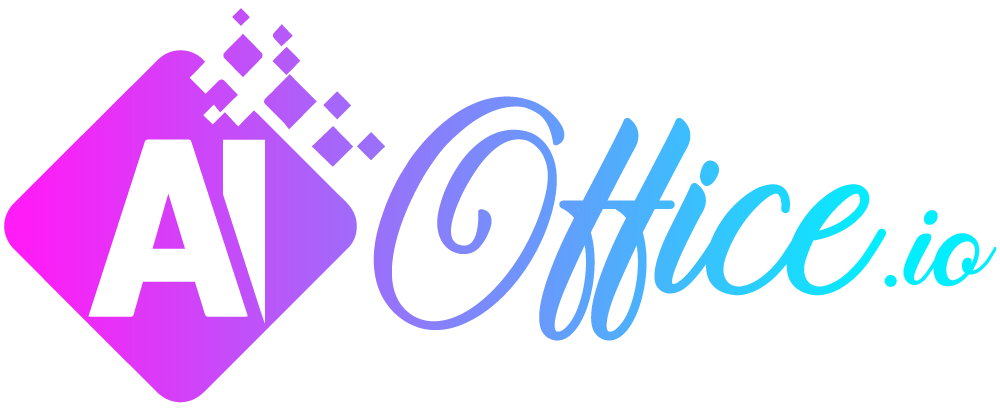
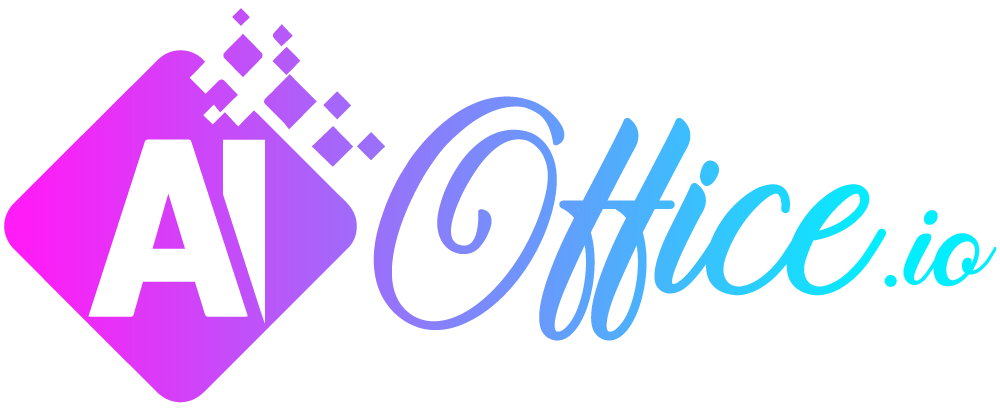
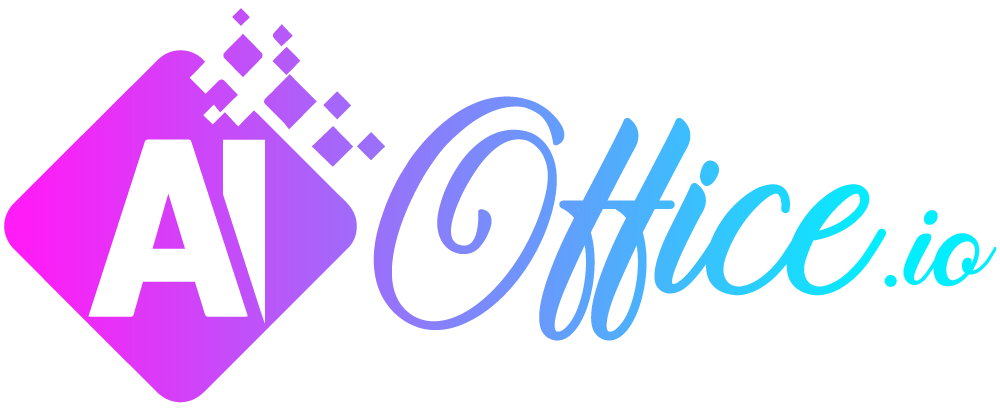
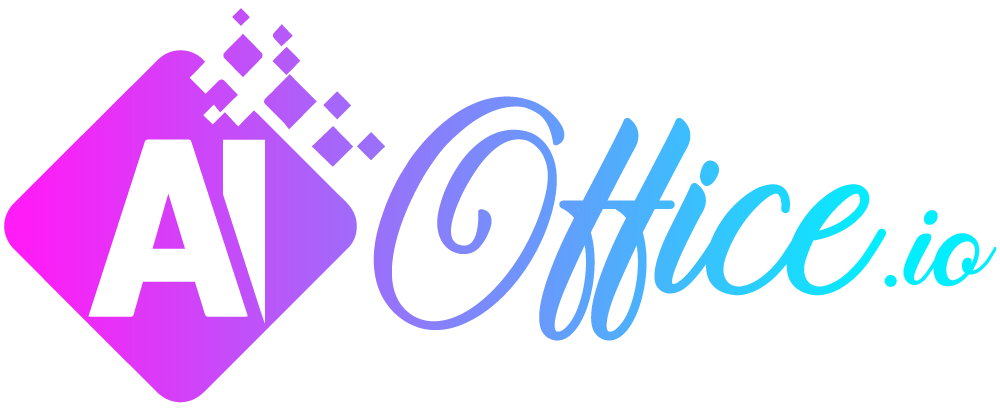
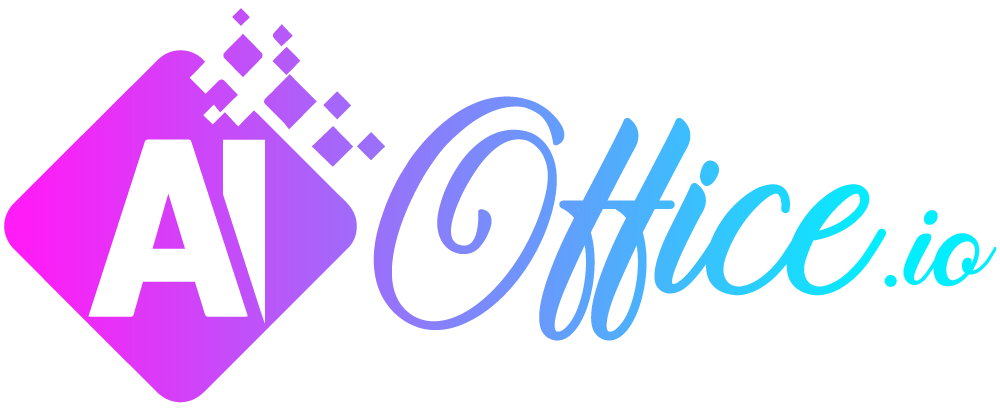
Operational technology started with simple devices and tools during the Industrial Revolution. Over the period, it moves to use electric management, and computers for more helpful automation, with the upgrade of the internet. OT system started linking with it for improved monitoring and managing.
Today, it uses smart technologies like IoT and AI to make industrial functions more efficient and connected.
What is Operational Technology (OT)?
The technology related to the detection of a shift driving a change using hardware and software is described as Operation Technology. This shift can either be via direct custody or monitoring of hardware. Like valves, detectors, I/O devices, controls, PLCs, actuators, switches, etc.) and software (customized and machine-specific).
Along with the parts mentioned above. OT methods employ a broad scope of control parts that act together to earn an objective, unlike other information processing systems. Any shift in an OT web has its effect in the real world. Owing to this, safety and safety are of paramount matter in OT systems, conflicting with security plans and functions frequently.
Types of Operational Technology
Operational Technology (OT) systems contain a range of technologies used to scan. And control physical methods, devices, and infrastructure in industrial and vital conditions. Here are some other types of OT systems:
Supervisory Control and Data Acquisition (SCADA) Systems:
- Function: SCADA methods are used for monitoring and controlling industrial functions. They collect real-time data from detectors and devices, process it, and supply operators with the ability to control functions remotely.
- Applications: Utilities (electricity, water, gas), manufacturing, transport.
Distributed Control Systems (DCS):
- Function: DCS are used for operation control in industrial settings. They spread control functions across multiple controls to manage complex operations. And provide high levels of dependability and sameness.
- Applications: Chemical processing, fat and gas refining, power years.
Programmable Logic Controllers (PLCs):
- Function: PLCs are powerful computers used for automating machinery and methods. They are designed to execute real-time control and scanning tasks based on a programmed reason.
- Applications: Manufacturing mechanization, group lines, packaging.
Building Management Systems (BMS):
- Function: BMS manages and controls, making systems similar to HVAC (heating, ventilation, and air sports), lighting, and safety systems. They improve power efficiency and ease within structures.
- Applications: Commercial buildings, industrial buildings, and large residential complexes.
Manufacturing Execution Systems (MES):
- Function: MES controls and monitor work-in-progress on the plant floor. They bridge the gap between firm resource planning (ERP) methods and control systems, supplying real-time data on production.
- Applications: Discrete manufacturing, batch processing, meals and beverage show.
Operational Technology (OT) Security for Industrial Companies
There is a massive need for rigorous OT security and vital infrastructure systems. And that must grow exponentially in the future years as the number and severity of episodes on our critical infrastructure systems grow. For example, industrial institutions have become routine marks of ransomware, supply-chain and other episodes.
IBM’s 2022 X-Force Threat Intelligence Index wrote that manufacturing was the most-targeted drive in 2021, as threat actors aspired to “imprison companies” and “fracture the spine of global supply chains” via ransomware and other exploits. Unpatched software was the most customarily exploited exposure, donating to 44% of ransomware attacks.
About half (47%) of attacks overall involved exposures that the victim company either had not or could not fix. Attacks on vital infrastructure, going from fuel pipelines to clinics, put lives at chance in addition to driving economic and social harm and potentially threatening national protection.
OT security manages the defects in OT systems, including older plans that have gone unpatched or, in some chances, are so old that they are not extended supported and thus can’t be fixed. Many systems, for example, still run Windows XP.
Other exposures include weak control over certificates (a favorite target of attackers), a lack of web segmentation and protocol isolation, and unsure relationships with IT systems, which are often used as access points.
Future Trends and Innovations in Operational Technology
Operational Technology is rapidly growing, combining advanced technologies to improve industrial efficiency and brightness. A key trend is the growing power of the Web of Things (IoT), which attaches physical machines to the Internet for state-of-the-art data exchange and study.
This integration rules to more intelligent, more connected industrial settings, allowing for small monitoring and improved function optimization. Further driving this change are advances in Artificial Intelligence (AI) and Machine Learning (ML).
These technologies allow OT systems to explore vast data sets, place patterns, and expect outcomes. This stuff is particularly transformative in predictive care, where AI forecasts gear failures, decreasing rest.
Also, intelligent automation, combining robotics and AI, is revolutionizing task performance, directing higher productivity and enhancing safety. Together, these creations are steering OT towards a future of intelligent, self-regulating systems, fundamentally changing industrial processes.
Networks and Connectivity in Operational Technology
Connectivity is vital in modern OT systems. Networks in OT promote contact between various hardware parts and software systems. This can be via wired relations like Ethernet or wireless technologies like Wi-Fi and Bluetooth. The web ensures that data courses seamlessly from detectors to buttons and then to actuators, as well as to monitoring devices for human direction.
In current years, the movement toward the Industrial Internet of Things (IIoT) has also emphasized the matter of connectivity in OT, permitting more integrated, intelligent, and responsive plans.
Hardware and Software Used in Operational Technology
The hardware in OT contains devices like detectors, actuators, and controls.
Sensors: Detect environmental guidelines similar to temperature, force, or activity.
Actuators: Complete physical moves based on commands, similar to moving parts or portal valves.
Controls: Machines like Programmable Reason Controllers process data from detectors and instruct actuators.
This hardware forms the material spine of OT, enabling real-time exchange and control of industrial functions.
Software Components
Software plays a role in managing and monitoring processes. Essential software parts are:
Control System Software: Programs controls to respond to detector inputs and control actuators.
Monitoring Tools: Supply user interfaces for real-time information visualization and manual management.
The software provides that OT plans are not only automated but also effortless and efficient, permitting human management and intervention when vital.
What Are The Risks?
The technical nature of OT points that systems are exposed to specific cyber risks that may not be used in IT environments. They contain:
- Use of legacy, unsure transmission protocols
- Traders that don’t pay sufficient heed to openness control
- Hardware lifecycles of 10+ years, denoting admins are forced to run obsolete OSes/software
- Patching challenges, as tools often can’t be taken offline to test updates (even if they are public)
- Tools that are too old to deploy current security solutions to
- Security diplomae that don’t identify severe defects, providing admins a false feeling of safety
- Security-by-design issues that existed reported/set CVEs, saying they fly beneath the radar
- Siloed IT/OT groups, which can make gaps in visibility, security and detection
- Doubtful passwords and misconfigurations (although this is also typical in IT domains)
From a specialized perspective, the Forescout report cited before highlights several types of openness in many OT effects:
- Unsure engineering protocols
- Weak cryptography or broken authentication methods
- Insecure firmware updates
- Small code performance (RCE) via born functionality
Conclusion
Operational Technology (OT) rules and monitors industrial processes, and it's currently operating closely with IT systems to grow efficiency and real-time data use. However, this mix also creates new cybersecurity risks that need a careful watch. While creations like IoT and AI enhance operations, they also require following complicated rules. Looking on, OT will continue to grow with new technologies, showing both advantages and challenges for companies.