What Are The Important Core Functions Of Operations
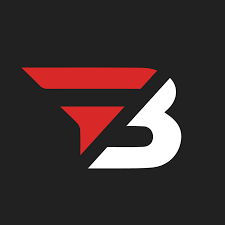
Admin
AI Research Analyst | 22 February 2025Table of Content
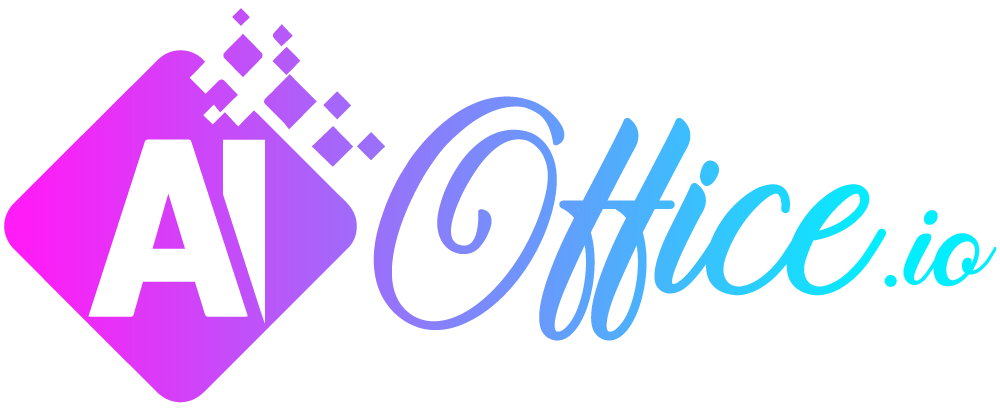
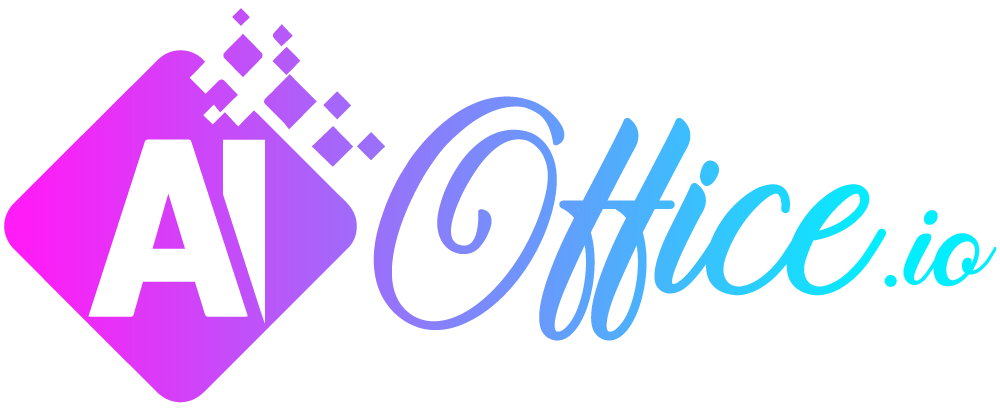
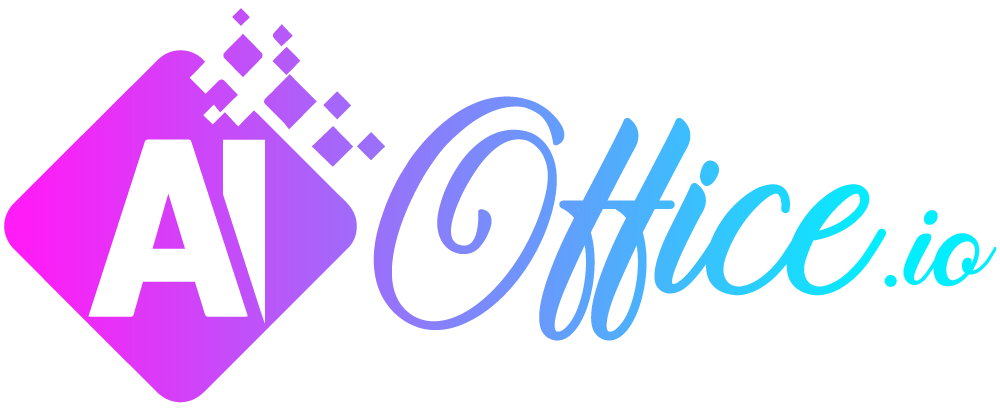
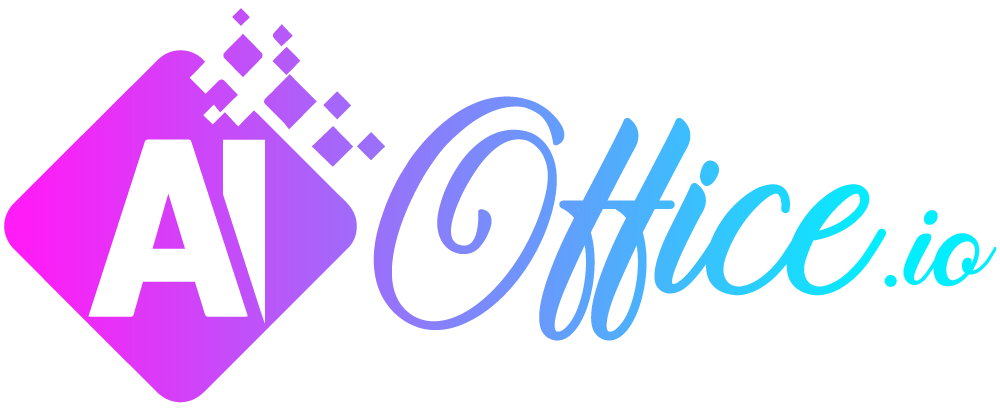
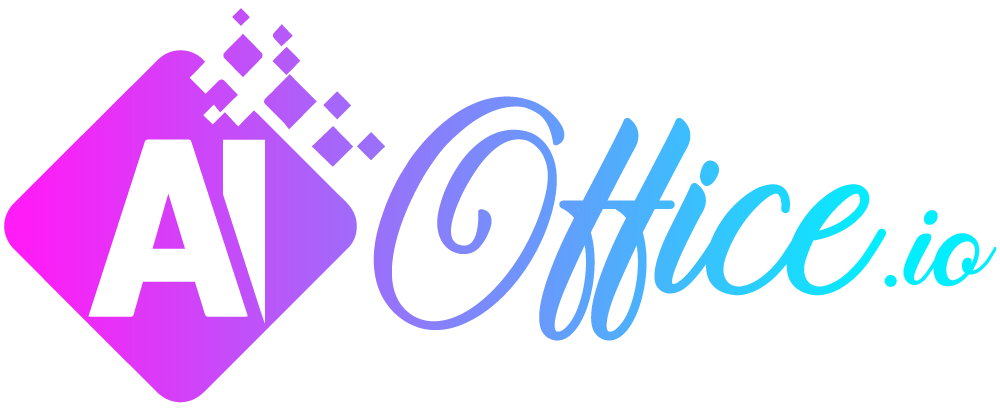
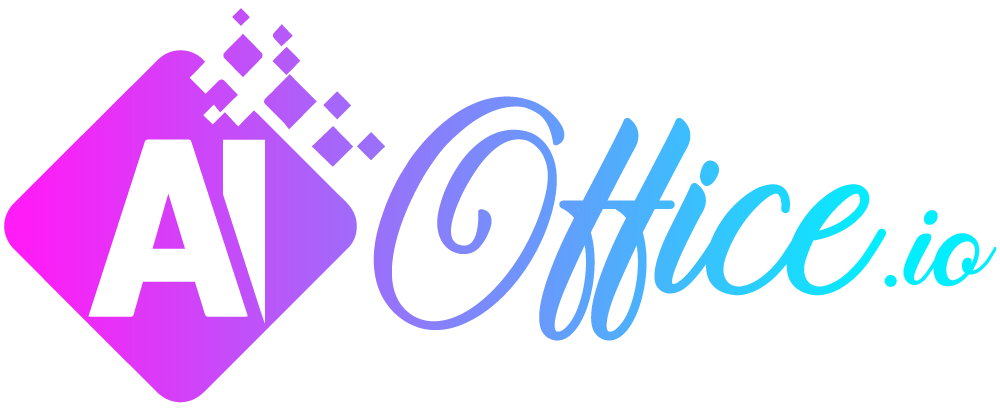
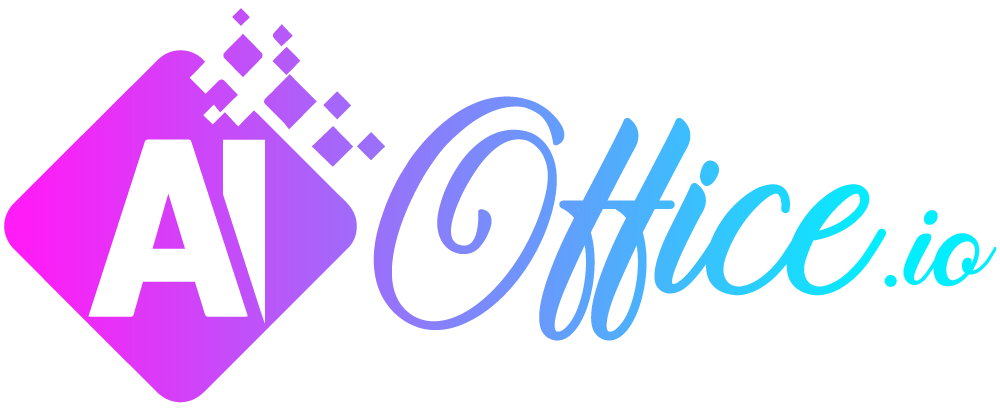
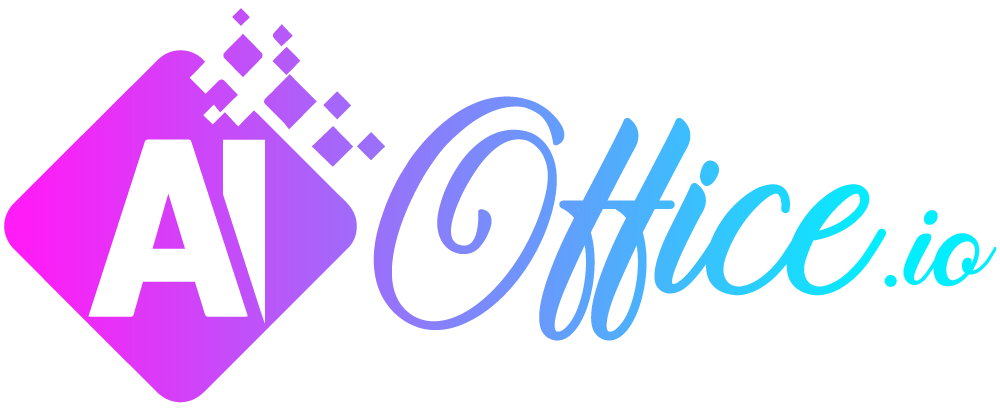
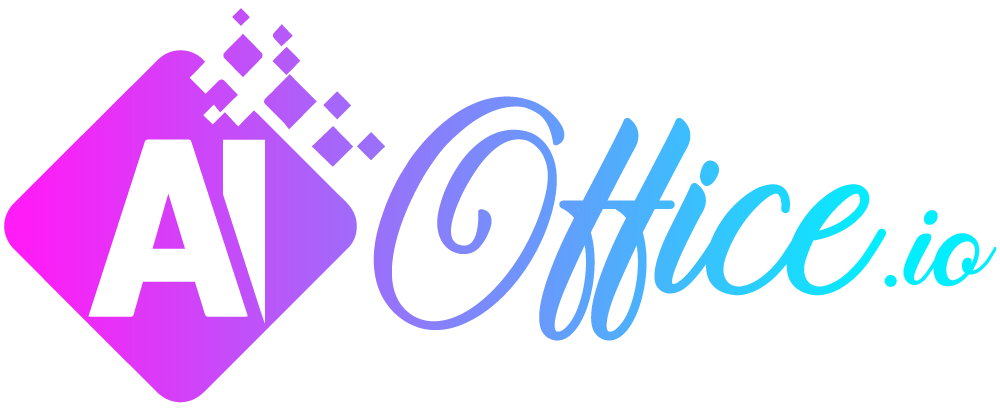
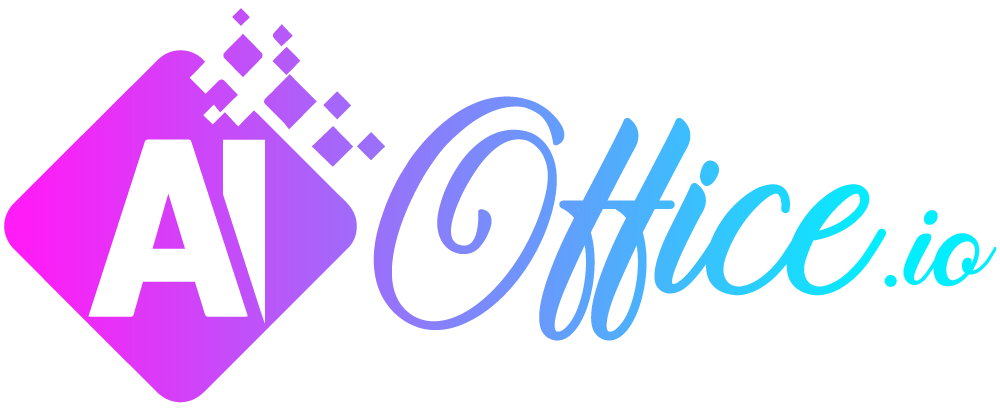
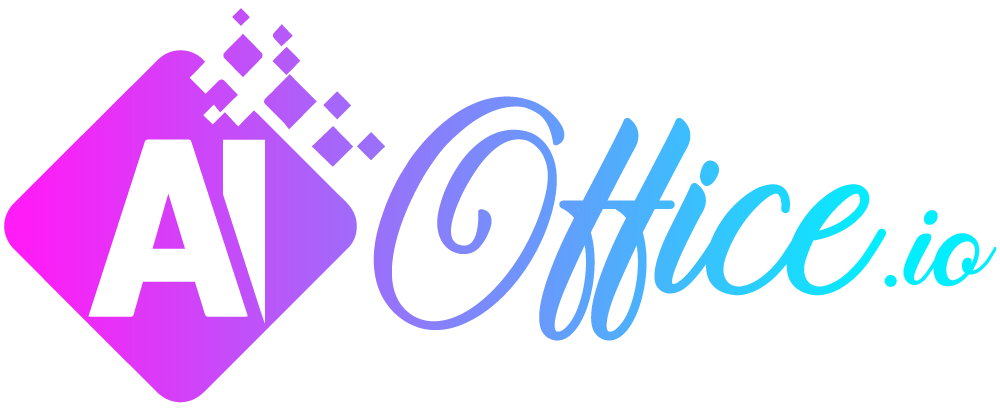
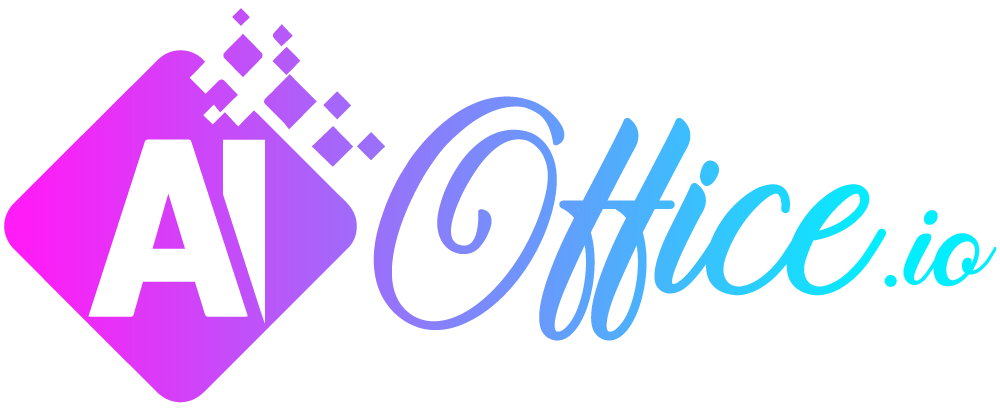
Operational management is like considering your company as a busy restaurant, where multiple groups of chefs and cooks are responsible for multiple operations. So, as an operational manager, you are responsible for the whole operation management, which chef is responsible for which task and how things are performed in the restaurant. What are the core functions of operation management, and what challenges does an operational manager face? Let's discuss everything in detail.
Purpose Of Operations Management
The main purpose of operation management is to get good output from input. Its primary aim is to utilize resources effectively so that the required input can be achieved. This involves planning, organizing, and many other aspects that are suitable for the smooth operation of an organisation.
Another purpose is to ensure that productivity does not stop. Let's discuss its 7 core functions, how they are helpful, what challenges are faced in them, and how these challenges can be resolved.
7 Important Core Functions Of Operations Management ( Challenges & Solutions )
Supply Chain Management
It is the backbone of modern business; how modern businesses deliver th raw materials to the end customer all depends on the operation management. They manage customer relations and provide them the quality products. There are much software that helps an operation manager track the delivery schedule and everything regarding the supply chain. So, it's a foremost function of operation management.
Challenges
One of the main issues here is the increase in global uncertainties. its really important to select the supply routes carefully because even a small incident can change the whole supply chain management process. Changes in the price of fuel and other things also cause unclear delivery.
Change in weather = change in delivery schedule. Limited visibility throughout their supply networks is another issue that many businesses face, which makes it challenging to identify and address issues before they have an impact on output.
Solutions
Most companies use the latest technologies to strengthen their supply chain, like:
- Artificial intelligence
- Internet of things
- Cloud computing
- Robotics
- Supply chain security
- Automation
There are many teaching systems available for it, and many teaching systems help to understand the shipment pattern in real life; they can quickly respond to delays.
Good relations with other supplies provide many backup options when an issue arises. Also, forecasting options are available. Many businesses use forecasting tools to predict future analysis, which helps them to make strong decisions for the future.
Quality Control
Quality control has gone way beyond basic product inspection. Contemporary quality management is about developing systems that do not allow defects to occur at all. Operations managers need to formulate precise quality standards, instruct employees to keep up these standards, and adopt checking procedures in the course of the production process. This active approach catches mistakes early on, preventing waste and ensuring customer satisfaction.
Challenges
Sometimes, products will become more complex, and with complex and large products, the client's requirements will increase, which makes it difficult to meet the expectations of the product. If a business trains new customers, it takes time as well as resources. Many companies do not even have enough budget to meet the requirements of the user, and the main reason is pressure on companies.
- High competition
- Low cost
- A lot of customer demand
Solutions
High-performing companies fight quality issues with both technology and training. Computerised inspection systems (computer vision technology) are capable of inspecting products faster and more uniformly than human inspectors. Periodic worker training programs ensure all workers know about quality standards and processes.
Analysis of data informs managers of patterns in quality issues so that they can repair problems at their source. Most companies also establish quality circles in which workers can exchange suggestions for better product quality.
Process Improvement
Process improvement means that you shouldn’t just look at your results when you reach your destination but rather check the quality at every step. Operation managers observe at each step how they can move to the next step and perform even more efficient functions.
Businesses can gather feedback in different ways; they can receive feedback from users or customers.
Success in process improvement = necessary changes + maintaining stable operations.
Many successful companies follow this methodology, including Toyota, McDonald's, and Southwest Airlines.
Problems & Solutions
4 Major Barries of Process Improvement:
- Resistance to change is one of the greatest barriers to process improvement.
- Employees and managers are used to the current way of doing things and might not want to change.
- Limited budgets will make it hard to put improvements into place, particularly those that involve new equipment or training.
- Measuring the real effect of changes to the process can also be difficult, which makes it difficult to make improvements a priority.
Solutions
Effective process improvement begins with the development of a culture open to good change. Workers must be engaged in finding and implementing improvements by managers, and thus, they are made partners, not victims, of change. Small, tangible improvements begin first, establishing credibility and momentum for larger change.
New tools of data gathering and analysis make it possible to measure the effects of improvements, yielding clear evidence of their worth. Frequent training and communication establish a climate of understanding and acceptance of improvement programs.
Forecasting in Operations Management
Forecasting plays a very important role in operation management. Lforcasting may not be helpful today for the future to check future predictions. Nothing is perfect other than this function. For example, if a company wants to sell ice cream in October, what will this feature do? It will check the previous year, how much ice cream was sold in October, and what type of audience it is. It helps a company to find out whether it should sell ice cream in the future or not.
Current Challenges
Due to fast customer changes and preferences, it's really hard to get the exact forecasting information from previous information.
The rise in prices is also a main factor; for example, if a customer bought an ice cream last year in 100, but future, the prices of raw materials will increase. The customer will check the same ice cream in 100, but at the same price, it will not be possible to produce the same product.
Practical Solutions
Contemporary companies address forecasting issues with the help of sophisticated analytics tools and improved data management. Machine learning algorithms can detect patterns that may ignore humans, while real-time data capture allows for current information.
BEST Forecasting Tools In 2025
- Sales forecasting software
- Time series models
- Econometric models
- Judgmental forecasting models
Product Design
Product design is a complex process finding a balance among customers' demands, manufacturing facilities, and corporate goals. Product design today implies close collaboration between designers, engineers, and producers.
Operations managers need to develop new products that are efficiently manufactured while complying with quality and cost requirements. The process may involve prototyping, testing, and ongoing refinement through feedback. Feedback sessions assist with guaranteeing the designs address true market requirements.
Current Problems
There are several problems with product design today. Material costs are up and it’s hard to design affordable products without sacrificing quality. Environmental regulations require more sustainable design. Companies struggle to balance innovation with manufacturing. when using new technologies or materials. Meeting customer needs while keeping processes simple is a big problem.
Practical Answers
Successful companies solve design problems with integrated thinking. 3D modeling and simulation tools test designs before expensive prototypes are built. Cross-functional teams get all the perspectives early in the design process. Many companies are now using modular design principles, designing products that share common components to reduce complexity. Customer feedback sessions regularly to ensure designs meet real market needs.
Final Words
The best companies know these functions don’t work in isolation. They work together as a system, each one supporting and enhancing the others. Companies that master these core functions and can adapt to change position themselves for long-term success in a competitive global market.